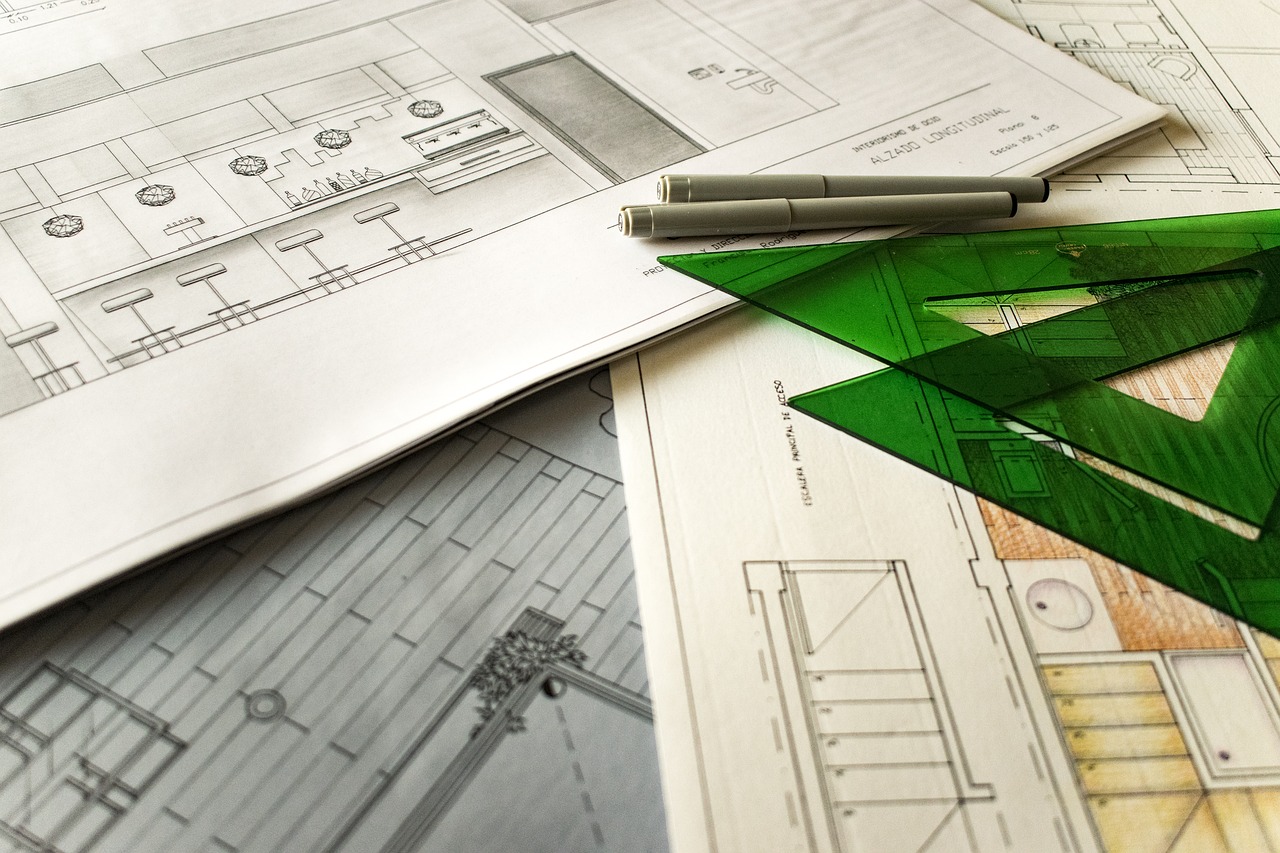
Autodesk officially revealed the AutoCAD 2019 new features…and you’re gonna want to see them.
These changes reveal a new direction for Autodesk and attempt to accomplish a few different goals:
- Simplify the AutoCAD software package
- Increase the value they deliver to their subscribers
- And allow engineers to work and collaborate online seamlessly.
We’ll show you how they accomplished those goals with the new features in AutoCAD 2019.
The Top 5 AutoCAD 2019 New Features
Specialized Toolsets Bundle
This is the most noticeable change in AutoCAD 2019.
Autodesk moved away from offering a variety of software products to bundling their core verticals into a single subscription to AutoCAD 2019 – known as One AutoCAD.
Now you get access to 7 specialized toolsets in addition to AutoCAD 2019:
- Architecture (previously known as AutoCAD Architecture)
- Mechanical (previously known as AutoCAD Mechanical)
- Electrical (previously known as AutoCAD Electrical)
- Map 3D previously known as AutoCAD Map 3D)
- MEP (previously known as AutoCAD MEP)
- Raster Design (previously known as AutoCAD Raster Design)
- Plant 3D (previously known as AutoCAD Plant 3D)
These toolsets allow you to expand the work you do at no additional cost apart from your initial subscription.
DWG Compare Tool
The new DWG Compare tool is one of the most exciting new features in AutoCAD 2019.
The old Drawing Compare tool from AutoCAD Architecture was good, but it didn’t have the functionality or flexibility that the new DWG Compare tool has.
DWG Compare does the same thing as the old Drawing Compare tool – compare two versions of the same drawing. But DWG Compare offers greater control over this process in the following ways:
- You can specify which colors are used to identify the differences between the versions you’re comparing.
- You can control whether text should be included or excluded from the comparison.
- You can place a revision cloud around a single change or a group of changes.
- And running DWG won’t alter your existing files. Instead, the comparison will be shown in a third drawing.
These new functions breathe new life into the Compare tool and make it even more useful than it was before.
Shared Views
The traditional way of collaborating on designs required you to convert your DWG file into a PDF to share with your teams.
With the Share View tool, you can share your designs with stakeholders within or outside your company without releasing your original drawing files.
AutoCAD 2019 hosts the design in the cloud, generates a shareable link, and lets project stakeholders view, review, measure, comment, and markup the drawing in their own web browser.
This streamlines the previously clunky process of using different file formats to get feedback on your designs.
And all the feedback you receive is saved in the file you share and can be implemented on your own AutoCAD desktop application.
AutoCAD Web App
This feature of AutoCAD 2019 isn’t an upgrade, it’s a completely new way to use the software.
It’s the first time you’ll be able to access, perform, and share your drawings directly from the web – no installation required.
Just go to the web app and login and you can start working from anywhere.
Here are the key features of the web app:
- DWG file access (Share View)
- Core 2D Drafting and Editing Tools such as Polyline, Arc, Revcloud, Offset, Trim, and Dimension
- Original AutoCAD Technology that provides the same authenticity and precision as the desktop version of AutoCAD 2019
With so many similar features, the AutoCAD web app could be a replacement for the desktop version in the near future.
AutoCAD Mobile App
Why stop at a web app when you can create a mobile app, too?
With the AutoCAD mobile app, you can view, edit, create, and share CAD across Windows, Android and iOS phones and tablets.
The mobile app was designed for users working on-site and features a few mobile-only tools to enhance the power of AutoCAD in the palm of your hand, such as:
- DWG File Access which gives you full access to your rich DWG files from the cloud and also allows you to download DWGs onto your device so you can work offline without internet connectivity.
- Magnifier and Object Snap which lets you make accurate edits and measurements.
- Quick Trim and Measure which lets you make quick edits with a single tap on the screen.
- Laser Measurements which lets you take measurements using the Leica DISTO by connecting your mobile device via Bluetooth.
- Annotations and Photo Attachments which enable you to log quick observations from the field using annotation tools like shapes, arrows, text, highlights, and photos directly on your drawings.
How to Buy AutoCAD 2019 (and How Much it Will Cost)
Since Autodesk is bundling 7 toolsets with AutoCAD 2019, it makes sense to raise the price – which they did by about 7%.
Instead of the $1,470 per year subscription you may be used to, the new AutoCAD subscription price is $1,575 yearly, and $195 monthly, which you can check out here.
How to Download AutoCAD 2019 for Free
If you’re not sure AutoCAD 2019 is right for you, get a free trial here.
What Should You Do after Getting AutoCAD 2019?
Upgrade your AutoCAD skills, of course.
If you want to get better with AutoCAD and any of its included toolsets, we got you covered.
From the beginner basics to the expert secrets, we’ll help you master AutoCAD 2019.
You can check out all of our AutoCAD programs by signing up for a free trial below.
Experience the proven, easy-to-use, and cost-effective benefits of online training by starting your free trial of our Autodesk AutoCAD training today!